Have you ever pondered the financial investment required to transform a virtual concept into a tangible, physical entity? The advent of 3D printing has unlocked a plethora of opportunities in crafting bespoke items, developing prototypes, and fabricating functional components. However, the expense associated with 3D printing can fluctuate significantly due to numerous variables, including the model of the printer and the materials employed. This piece aims to dissect the diverse factors influencing the cost of 3D printing, enabling you to gain a comprehensive understanding of the financial implications involved in materializing your 3D innovations.
Deciphering the True Price: Purchase and Operation of a 3D Printer
3D printing is revolutionizing various industries, from medical to automotive. But before jumping headfirst into this transformative technology, aspiring enthusiasts or entrepreneurs must understand the full financial commitment. The cost of buying and running a 3D printer plays a significant role in determining the overall expenses related to 3D printing.
Investment in a 3D Printer: Initial Costs
3D printers come in a wide range of prices, starting as low as $200 and escalating to $150,000, depending on the technology and features. Factors like printing speed, resolution, materials compatibility, and build volume significantly influence the price.
While a hobbyist might find a $200 printer sufficient, a business that demands high-quality prints with intricate detailing might need to invest in high-end printers, which might cost tens of thousands of dollars. But purchasing the printer is just the beginning of your financial investment.
Running Costs: Operating a 3D Printer
Operating costs can add up quickly and should be considered when calculating the total cost of 3D printing. Let’s illustrate this with an example:
Assume you have invested in a mid-range 3D printer, which cost you $1,500. Your plan is to operate this printer for around 8 hours a day for two years, equaling a total of 5,840 operational hours.
Simply, divide the cost of your printer with these total hours:
$1,500 ÷ 5,840 hours = approximately $0.21 per hour
This implies that if a 3D model takes about 4 hours to print, you would add approximately $0.84 to your base price to cover the cost of your machine operation.
In the real scenario, operating costs are never this straightforward. They involve other factors like energy consumption, maintenance costs, software costs, and more. But this simplified calculation provides a good starting point to understand the long-term expenses of running a 3D printer.
Thus, the time and resources invested in 3D printing significantly impact the overall cost. It’s not simply about buying the printer; it’s about calculating and covering all the running costs associated with it. Crucially, understanding these factors will help you price your 3D printed products appropriately, ensuring a viable and profitable 3D printing venture.
The Need for 3D Models: The Core of Accurate Quotations
The importance of the 3D model in the 3D printing process cannot be overstated. “Share your 3D model with us,” is typically the second statement a 3D printing service provider makes, following the initial “it depends” discussion. Without a 3D model, giving an accurate estimate for a 3D printing project becomes a Herculean task, even for the most experienced industry veterans.
The 3D model provides crucial information used in determining all the parameters that contribute to the printing cost. Hence, understanding the key elements of a 3D model that affect the cost is vital.
Analyzing Model Volume
By having a 3D model, the service provider can calculate essential elements such as the total volume of the model and other generated supports. The total volume is particularly important as it directly impacts the amount of material needed to print the model – simple math, the larger the volume, the higher the material usage and thus, the higher the cost.
Here are a few strategies to manage volume and consequently, cost:
- Hollow Out Your Model: One effective way to keep the cost down is by hollowing out the model wherever possible. This significantly reduces the volume of material needed for printing, thus cutting down the cost;
- Design Models Wisely: Surprisingly, a model with larger dimensions (like a 3ft model) can have less volume than a smaller one (like a 1ft model). If the smaller model is designed solid and the larger one is hollow, the larger model becomes more cost-effective;
- Opt For Efficient Support Structures: Try to design models that require less supporting structure. This way, you will use less material, reducing volume and cost.
Given the direct impact of a 3D model’s volume on the cost, it’s easy to see why getting an accurate price for 3D printing without a 3D model is akin to shooting in the dark. Understanding these factors and using strategies to optimize volume can help control 3D printing costs, making the process more economically viable and profitable.
Complexity in 3D Models: When Human Intervention Prevails Over Algorithms
In the magical world of 3D printing, every project is not the same – a fact that holds particularly true when it comes to 3D models. Some models are 3D-print-ready, perfectly designed with the right specifications and accurate measurements. However, some models are a complete puzzle, laden with complexity and requiring significant adjustments before they can be 3D printed.
There’s no denying that the age of automation has made transactions faster and smoother in many sectors, including 3D printing. Especially for simple products, automated 3D printing services are an excellent solution.
The Intricacies of Complex Projects
However, the question arises – What about complex components and architectural models? This is where human intervention becomes crucial, even with the most advanced algorithms in place. Complex 3D printing projects often involve intricate designs that may have problem areas, which aren’t easily detected by automated systems.
Imagine a scenario – A customer submits a 3D model of a full-scale stadium they want to print in 3D. Upon close inspection of the file, it’s found that the model is riddled with issues – loose joints, excessively thin walls, and even 3D models hidden within the stadium structure itself.
Attempting to 3D print such a file right off the bat would lead to a significant waste of material, potentially racking up thousands of dollars in unnecessary costs.
The Need for Expert Review
This scenario underscores the importance of expert assessment and intervention in 3D printing projects, especially those involving intricate designs. It places the spotlight firmly on a significant question – Do you want to risk printing your 3D model as is, despite the potential problems that might surface during the printing process? Or do you prefer to ensure your final print meets, if not exceeds, your expectations?
Here are some tips for dealing with complex 3D models:
- Engage Expert Services: Consider engaging the services of a professional 3D printing service that employs a team of experts to review and optimize your 3D models before printing;
- Prepare for Iterations: For complex models, iterations are a part of the process to achieve the perfect output. Be prepared to tweak and modify your model based on expert feedback;
- Quality over Speed: While automation accelerates the 3D printing process, it might not always deliver the desired quality, particularly for complex projects. Prioritize quality over speed for the best outcomes.
Complexity adds a layer of challenge in 3D printing. However, with the right strategies and a bit of expert human touch, you can successfully navigate these complexities and achieve the perfect 3D print, every time.
Material Choices and Their Impact on 3D Printing Costs
Material selection is a pivotal aspect that shapes the cost, quality, and outcome of any 3D printing project. The spectrum of available materials is vast, but here, the focus will primarily rest on two popular choices: thermoplastics and resin.
Thermoplastics: Filaments and Powder
Cost: Low ($)
Even beginners exploring the realm of 3D printing would be familiar with terms such as “ABS” or “PLA.” They are the most commonly used 3D printing materials, and there’s a reason for their popularity. Thermoplastics like ABS and PLA are a cost-effective choice for hobbyists and beginners mastering the basics. Typically, prices for these filaments vary between $20 and $70 per kilogram, making them a pocket-friendly option.
However, their affordability comes with a caveat. While they are wallet-friendly, achieving a high-quality 3D print from these materials can be challenging. It often includes hours of post-processing to obtain a smooth finish. Also, using thermoplastics to 3D print complex models might hit a roadblock due to the material’s limitations.
Tips for working with thermoplastics:
- Practice Patience: Remember, achieving smooth finishes will require patience and hours of post-processing;
- Start Simple: For complex models, consider starting with a simpler model or consider different materials.
Thermosets: Resin
Cost: High ($$$)
Resin holds a reputation as one of the best 3D printing materials for its versatility and the superior quality of 3D prints it produces. Whether the project is complex or simple, resin can handle it all, but its versatility does come at a cost. Standard resin costs around $50 per litre on average, while some specialised resin materials can reach up to $300 per litre.
The higher cost of resin is often justified by the fine detail, superior finish, and the range of applications that resin-based 3D prints offer.
Tips for using resin:
- Invest Wisely: For high-end projects demanding exceptional quality, investing in resin could be worth it;
- Explore Bulk Purchase: If a project requires a large volume of resin, consider partnering with a 3D printing company with access to discounted prices.
Material selection is crucial in determining the cost, quality, and outcomes of your 3D printing projects. By understanding the strengths, limitations, and costs associated with different materials, you can make informed decisions that align with your project requirements and budget.
The Aftermath of 3D Printing: The Essential Role of Post-Processing
A common misconception is that 3D printing is a one-click process – simply upload, print, and the final product is ready to roll. However, the reality is that post-processing plays an integral role in refining 3D prints and ensuring they meet the necessary quality standards.
Post-processing involves several steps, such as curing, cleaning, and polishing the 3D printed object, ensuring it is not only aesthetically pleasing but also functional and durable.
Polishing – A Key Step in Post-Processing
The picture often shown of 3D printed objects is a smooth, shiny object, but the reality right out of the printer can be quite different. Especially for filament-based 3D printing, the object comes out rough and with visible layers. Polishing becomes a necessary evil to achieve the desired smooth finish.
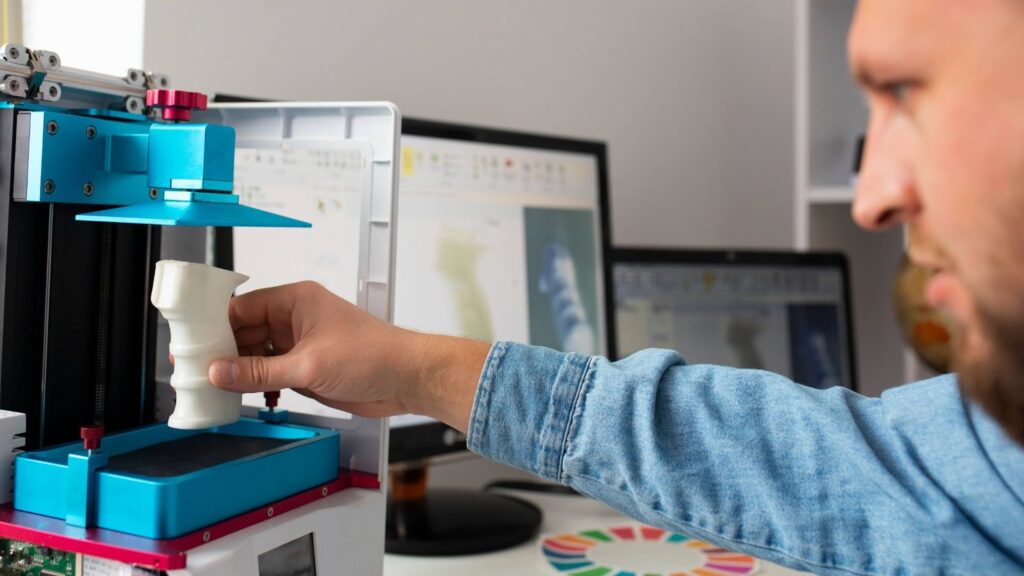
Filament-Based Prints
With filament-based prints, the polishing process can be daunting and extremely time-consuming. Removing supports and refining the rough surfaces is a painstaking task. It requires time and a great deal of patience. It’s worth considering if the outcome warrants the invested time and effort.
Resin-Based Prints
Resin-based prints, on the other hand, are comparatively simpler. After the UV curing process, these parts can be polished either manually or using a sandblaster, significantly reducing the time and effort required in post-processing.
Tips for Post-Processing:
- Weigh the Effort: If you are dealing with filament-based prints, gauge the level of polishing required and decide if the time invested will pay off;
- Seek Expert Help: If the intricacy of the model makes post-processing a challenge, consider enlisting the help of experts to ensure the final product meets your expectations.
Remember, the complexity of your 3D model could significantly affect post-processing. A complex model could generate supports that are challenging to clean, requiring a high degree of expertise and patience. Therefore, considering the post-processing requirements before embarking on a 3D printing project can help set realistic expectations regarding the final product’s cost and quality.
Enhancing Final Outputs: The Art of Finishing 3D Prints
While 3D printing technology has progressed leaps and bounds, there are still limitations to the finishes and color options available. Most 3D printers can’t accomplish sophisticated finishes like gold or chrome or meet specific Pantone color requirements. That’s where the art of finishing comes into play.
Finishing processes such as painting and metal plating are often required to achieve these desired appearances. By applying these finishing techniques, 3D printing services can deliver products that match the aesthetic expectations of their clients perfectly.
Calculating Profit Margins: The Lifeline of a 3D Printing Business
To sustain the business and ensure its growth, 3D printing companies need to factor in profit margins. Typically, these margins range from 50% – 90% of the material cost. It’s important to note that these are quite simplistic calculations that only consider the cost of materials.
When other overhead expenses and labor costs are taken into account, these profit margins shrink significantly. It’s important to understand that a good portion of the cost associated with 3D printing services is dedicated to covering these indirect costs.
The Essential Base Price
For any business, there’s a minimum charge to make the operation worthwhile. In the context of 3D printing, there’s a base price applied to orders below a certain value. For instance, it’s impractical for a company to process an order and operate the machinery for a $3 print.
This situation warrants either an increase in order quantity or an adjustment to meet the base price, which could be between $30-$90. Despite automation, labor involvement is unavoidable in 3D printing, and the base price helps cover those costs.
Here are some quick tips:
- Get Estimates: For projects requiring special finishes, request estimates including finishing costs;
- Understand Calculations: Ask the services about their pricing structure to understand what you are paying for;
- Bulk Orders: Consider placing bulk orders to make the most of your investment.
These considerations help keep the business afloat while ensuring the quality of the 3D printing service. The focus is not just delivering a 3D printed object but a refined product that mirrors the client’s vision and expectations.
Conclusion
Unlocking digital visions into tangible realities, 3D printing embodies a transformative power, yet its financial implications exhibit a wide spectrum. The cost spectrum spans from a mere handful of dollars for simplistic prints to an exponential surge into the realm of thousands for intricate designs utilizing industrial-grade materials. This piece delves into the pivotal facets that sway the financial scale of 3D printing, encompassing variables such as the printer’s type, the chosen materials, and the inherent complexities embedded within the model.
Gaining insights into these determinants empowers individuals to make judicious choices concerning investing in a 3D printer or opting for professional 3D printing services. It’s crucial to note that the financial equation doesn’t merely encompass the direct cost of the print. Considerations must extend to factors like electricity consumption, potential software expenses, and the inherent value of time when undertaking a comprehensive cost analysis.