In the world of additive manufacturing, 3D printing with metal has gained significant popularity for its ability to create complex and durable parts. However, one common question that arises when considering metal 3D printing is, “How much does it cost?” The cost of 3D printing metal can vary depending on various factors such as the type of metal printer used, labor costs, post-processing requirements, and the size and complexity of the model being printed.
Metal 3D Printers Costs
Metal 3D printers are a significant investment, with prices ranging from $400,000 to $800,000 for industrial-grade machines. These high-end printers are capable of producing large and intricate metal parts with high precision. However, for those looking for more affordable options, there are smaller office-friendly models available for around $120,000. These smaller printers are suitable for small businesses or research institutions looking to get started with metal 3D printing.
Labor Costs and Post-Processing
Labor costs associated with metal 3D printing can vary depending on the printing system used and the safety requirements involved. Some metal printing processes may require more manual labor and monitoring, leading to higher labor costs. Additionally, post-processing of metal 3D printed parts can also contribute to the overall cost. Methods like powder bed fusion may require expensive support structures or additional finishing steps, increasing the post-processing costs.
Total Cost Per Piece
The total cost per piece for 3D printing metal typically ranges from $15 to $800. This wide range in cost is influenced by factors such as the size and complexity of the model being printed, as well as the finishing requirements. Larger and more intricate parts will naturally cost more to produce, while simpler designs may fall on the lower end of the cost spectrum. Additionally, the choice of metal material used can also impact the overall cost of 3D printing metal parts.
Factors Influencing the Cost of 3D Printing Metal
Metal Material Costs
One of the primary factors influencing the cost of 3D printing metal is the material itself. Different types of metal powders come at varying price points, with some exotic metals costing significantly more than traditional options like stainless steel or aluminum. The cost of the metal powder used in the printing process directly affects the overall cost per piece, making material selection an important consideration for budget-conscious manufacturers.
Design Complexity
The complexity of the design being printed also plays a significant role in determining the cost of 3D printing metal parts. Intricate geometries or designs with internal cavities may require additional support structures or post-processing steps, adding to the overall production cost. Simple designs that can be printed without the need for extensive support materials will generally be more cost-effective to produce.
Production Volume
The volume of parts being produced can impact the cost of 3D printing metal. While the initial setup costs for metal 3D printing can be substantial, the cost per piece tends to decrease as the production volume increases. Manufacturers looking to produce a large number of metal parts may benefit from economies of scale, resulting in lower average costs per unit. On the other hand, small-batch production runs may be more expensive on a per-piece basis.
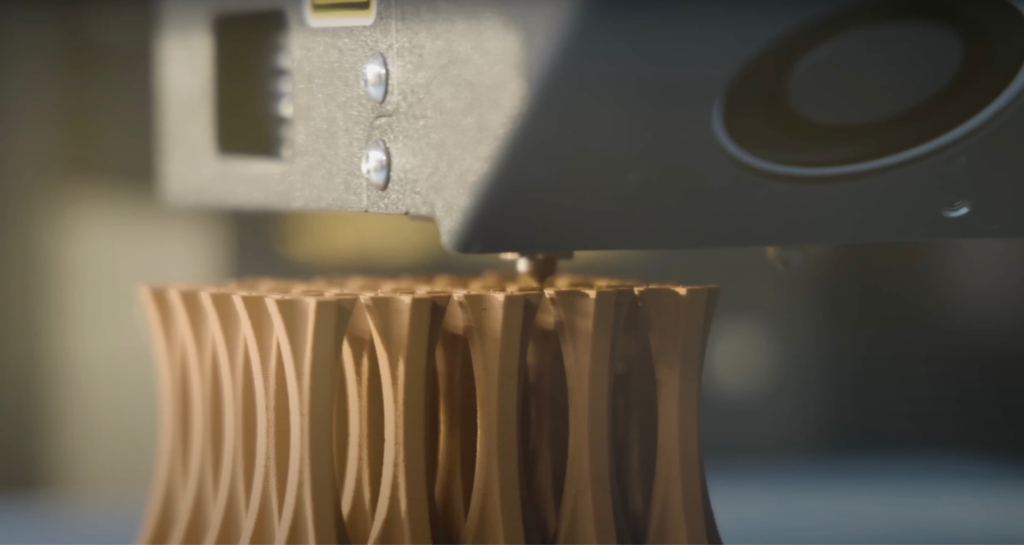
Comparison of Metal 3D Printing Technologies
Direct Metal Laser Sintering (DMLS)
Direct Metal Laser Sintering (DMLS) is a popular metal 3D printing technology that uses a high-powered laser to selectively fuse metal powder together layer by layer. DMLS offers excellent accuracy and surface finish, making it ideal for producing complex metal parts with tight tolerances. However, the cost of DMLS can be relatively high due to the specialized equipment and materials required.
Selective Laser Melting (SLM)
Selective Laser Melting (SLM) is another metal 3D printing process that uses a high-energy laser to fully melt and fuse metal powder into solid parts. SLM is known for its ability to produce dense and fully functional metal components, making it a preferred choice for aerospace and medical applications. While SLM offers superior mechanical properties, it can be more costly compared to other metal 3D printing technologies.
Binder Jetting
Binder Jetting is a metal 3D printing process that involves depositing layers of metal powder and a binding agent to build up a part. Once the printing is complete, the green part is sintered to remove the binder and fuse the metal particles together. Binder Jetting is a cost-effective option for producing metal parts quickly and efficiently, making it suitable for prototyping and low-volume production. However, the mechanical properties of binder jetted parts may not be as robust as those produced using other methods.
Metal 3D Printing Technology | Cost Range | Advantages | Disadvantages |
---|---|---|---|
Direct Metal Laser Sintering (DMLS) | High | High accuracy and surface finish | Expensive equipment and materials |
Selective Laser Melting (SLM) | High | Dense and functional parts | Higher cost compared to other methods |
Binder Jetting | Moderate | Cost-effective and fast | Lower mechanical properties |
Cost-saving Strategies for 3D Printing Metal
Material Optimization
Optimizing the design of metal parts to reduce material usage can result in significant cost savings during the 3D printing process. By minimizing unnecessary supports or adjusting the geometry of the part, manufacturers can reduce the amount of metal powder required, ultimately lowering the overall production cost. Material optimization techniques such as lattice structures or hollowing out components can help achieve cost-efficient metal parts without compromising on strength or performance.
Batch Production
Batch production is a strategy that involves grouping multiple parts together in a single build to maximize the efficiency of the 3D printing process. By consolidating several components into a single print job, manufacturers can take advantage of the full build volume of the printer and reduce the cost per piece. Batch production is particularly beneficial for small to medium-sized parts that can be printed simultaneously without sacrificing quality or accuracy.
In-house Post-Processing
Bringing post-processing operations in-house can help control costs and streamline the production workflow for metal 3D printed parts. By investing in equipment for finishing, polishing, or heat treatment processes, manufacturers can reduce the reliance on external service providers and shorten lead times. In-house post-processing capabilities allow for greater flexibility and customization, enabling manufacturers to fine-tune the finishing of metal parts according to their specific requirements.
Conclusion
In conclusion, the cost of 3D printing metal can vary widely depending on factors such as the type of metal printer used, material costs, design complexity, and production volume. Industrial-grade metal 3D printers come with a significant upfront investment, while smaller office-friendly models offer a more accessible entry point for businesses and research institutions. Labor costs and post-processing requirements also contribute to the overall cost per piece, making it essential to consider all aspects of the production process when budgeting for metal 3D printing projects.