In the rapidly evolving landscape of manufacturing, hybrid techniques that merge traditional methods with cutting-edge 3D printing are transforming how products are designed and produced. This synergy offers unparalleled flexibility, efficiency, and innovation, bridging the gap between time-tested processes and futuristic technologies. But what exactly does hybrid manufacturing entail, and why is it gaining traction across industries? Let’s explore.
Understanding Hybrid Manufacturing
At its core, hybrid manufacturing integrates subtractive techniques—like CNC machining, milling, or casting—with additive manufacturing, commonly known as 3D printing. Subtractive methods involve removing material to shape an object, while additive manufacturing builds objects layer by layer, often using materials like polymers, resins, or metals.
Combining these two approaches allows manufacturers to capitalise on the strengths of each. Traditional methods bring durability, scalability, and familiarity, while 3D printing introduces flexibility, precision, and the ability to create complex geometries. The result is a streamlined process that reduces waste, enhances product quality, and expands creative possibilities.
Key Features of Hybrid Manufacturing:
- Improved Precision: Traditional machining refines 3D-printed parts to achieve tighter tolerances.
- Material Versatility: Hybrid processes support a broader range of materials, from metals to composites.
- Cost Efficiency: Reduces material waste by combining additive efficiency with subtractive refinement.
Applications of Hybrid Manufacturing Across Industries
The beauty of hybrid manufacturing lies in its versatility, making it a valuable tool in various industries:
Aerospace and Defence
In aerospace, the demand for lightweight yet durable components is ever-growing. Hybrid manufacturing enables the creation of complex parts—such as turbine blades or fuel nozzles—by 3D printing intricate designs and refining them with CNC machining. This reduces material waste and ensures the structural integrity of critical components.
Healthcare and Prosthetics
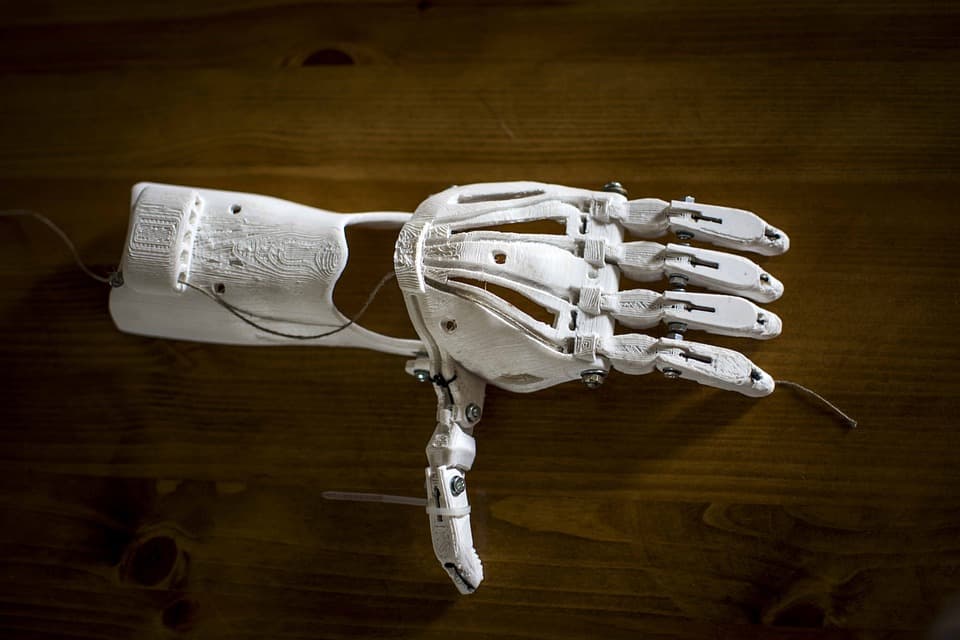
Customisation is key in medical applications. By leveraging 3D printing for tailored designs and traditional techniques for strength, hybrid manufacturing produces prosthetics, implants, and surgical tools that are both precise and robust. This approach is transforming patient care, enabling quicker production of life-saving devices.
Automotive Engineering
The automotive sector benefits from hybrid manufacturing through rapid prototyping and efficient production of customised components. For example, manufacturers can 3D print lightweight parts for electric vehicles and fine-tune them using conventional machining for optimal performance.
Artisanal and High-End Manufacturing
Hybrid manufacturing isn’t just about mass production—it also caters to niche markets like jewellery or luxury goods. Artisans use 3D printing for intricate patterns and then apply traditional polishing or casting techniques to enhance the final product’s aesthetic and tactile qualities.
The Benefits and Challenges of Hybrid Manufacturing
Benefits:
- Enhanced Efficiency: Hybrid systems reduce production time by eliminating the need for multiple separate processes.
- Design Freedom: Complex geometries achievable with 3D printing are further perfected using traditional methods.
- Sustainability: Reduced material waste aligns with growing environmental concerns in manufacturing.
Challenges:
- Equipment Integration: Merging additive and subtractive systems requires advanced software and expertise.
- High Initial Costs: Investing in hybrid systems can be expensive for small-scale manufacturers.
- Skill Gap: Workers must be trained in both traditional and modern techniques to maximise efficiency.
The Future of Hybrid Manufacturing
As technology advances, hybrid manufacturing will become even more sophisticated. Emerging trends include the use of AI-driven automation to optimise the blend of additive and subtractive techniques. For instance, machine learning algorithms can analyse design files to determine the most efficient manufacturing sequence, reducing human error and production costs.
Moreover, innovations in materials science are expanding the range of compatible materials for hybrid processes, including bioplastics and smart materials that respond to environmental changes.
Hybrid manufacturing is also paving the way for decentralised production models, where small-scale units can create high-quality, customised products locally, reducing the need for global supply chains. This shift could redefine manufacturing industries, fostering more sustainable and resilient economies.
Conclusion
Hybrid manufacturing is more than just a trend—it’s a revolution in how we think about production. By combining the precision and scalability of traditional methods with the flexibility and innovation of 3D printing, it opens the door to endless possibilities across industries.
Whether you’re an aerospace engineer seeking durable components or an artisan crafting bespoke jewellery, hybrid manufacturing offers a pathway to enhanced creativity, efficiency, and sustainability. Embracing this approach is not just about keeping up with the times; it’s about staying ahead of the curve in an ever-changing world.